The Role of Technology in House Construction
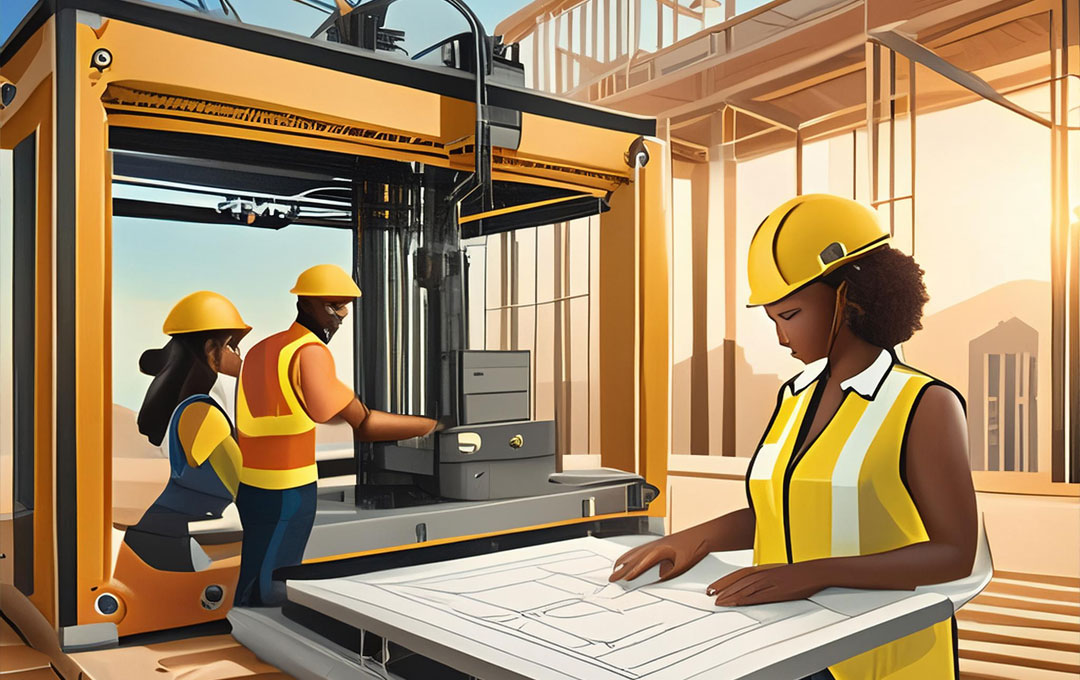
The Role of Technology in House Construction
In the past, building a house meant months of hard work, countless bricks, and endless blueprints. But now, thanks to cutting-edge technology, the way we construct homes is undergoing a seismic shift. Imagine machines that can print entire houses, architects who design in virtual worlds, drones that survey construction sites, and robots that handle heavy lifting—these innovations are not science fiction; they’re the reality of reshaping the house construction industry.
One of the most talked-about advancements is 3D printing. Instead of traditional methods, 3D printers use materials like concrete to build entire structures layer by layer, drastically reducing construction time and costs. Then there’s virtual reality (VR), where architects and homeowners can step into a digital realm to visualize and refine every detail of their dream home before a single brick is laid. On construction sites, drones soar above, capturing data and providing real-time insights, while robots work tirelessly to perform tasks that were once done by hand.
This blend of technology—3D printing, VR design, drones, and robotics—is not just changing how homes are built; it’s revolutionizing the entire construction industry, making projects faster, more efficient, and often more sustainable than ever before.
Let’s start with 3D printing
3D printing has emerged as a groundbreaking innovation in the house construction industry, fundamentally transforming the way buildings are designed and constructed. Unlike traditional construction methods that rely on assembling materials piece by piece, 3D printing allows for the creation of entire structures layer by layer, offering unprecedented speed, precision, and flexibility.
One of the key advantages of 3D printing in house construction is its ability to significantly reduce construction time. Traditional methods often involve lengthy processes such as bricklaying or concrete pouring, which can take weeks or even months to complete. In contrast, 3D printers can fabricate building components in a fraction of the time, dramatically accelerating the construction timeline. This not only saves time but also reduces labor costs and minimizes the disruptions typically associated with construction projects.
Moreover, 3D printing enables intricate and complex designs that would be challenging or impossible to achieve using conventional methods. Architects and designers can unleash their creativity, experimenting with innovative shapes, curves, and geometries that can enhance both the aesthetics and functionality of a building. This design freedom opens up new possibilities for creating unique, customized homes that reflect the individual preferences and needs of homeowners.
Another significant benefit of 3D printing is its potential to reduce waste and improve sustainability in construction. Traditional construction often generates substantial amounts of waste from excess materials, offcuts, and inefficiencies. In contrast, 3D printing can optimize material usage by precisely depositing only the required amount of material, minimizing waste and environmental impact. Additionally, 3D printing can utilize eco-friendly materials such as recycled plastics or sustainable concrete alternatives, further contributing to sustainable construction practices.
Furthermore, 3D printing offers enhanced structural integrity and durability. The layer-by-layer construction method allows for uniformity and consistency in material distribution, resulting in stronger and more resilient structures. This can lead to buildings that are better equipped to withstand environmental factors such as earthquakes, hurricanes, and other natural disasters, enhancing overall safety and longevity.
Overall, 3D printing is revolutionizing the house construction industry by streamlining processes, unlocking design possibilities, reducing waste, and improving structural performance. As this technology continues to evolve and gain widespread adoption, it has the potential to reshape the way we think about building homes, ushering in a new era of innovation and sustainability in construction.
Virtual reality is another game-changer
Virtual reality (VR) is revolutionizing the house construction industry by offering unprecedented capabilities in design visualization, collaboration, and decision-making. Architects, designers, and homeowners can now step into immersive digital environments that provide a realistic and interactive representation of a future home, transforming the way projects are conceptualized and executed.
One of the most significant benefits of VR in house construction is its ability to enhance design visualization. Traditionally, architects would rely on 2D drawings or computer-aided design (CAD) models to communicate their vision. However, these methods often struggle to convey the full spatial experience of a building. With VR, stakeholders can experience a virtual walkthrough of a proposed design, exploring every room, detail, and layout as if they were physically present. This level of immersion helps to ensure that design elements meet expectations and allows for early identification of potential issues or improvements.
Moreover, VR facilitates collaboration among project teams and clients. Design iterations and revisions can be seamlessly integrated into the virtual environment, allowing stakeholders to provide feedback, make adjustments, and visualize proposed changes in real time. This collaborative approach fosters better communication, alignment, and decision-making, ultimately leading to more refined and successful design outcomes.
Additionally, VR enhances the client experience by enabling them to participate in the design process actively. Homeowners can virtually walk through different design options, experiment with finishes, furniture layouts, and color schemes, and make informed decisions based on their preferences and lifestyle needs. This level of engagement not only increases client satisfaction but also reduces the likelihood of costly changes or misunderstandings later in the construction phase.
Furthermore, VR can streamline the approval and permitting process by creating digital simulations that showcase proposed designs within their intended context. Municipalities, regulatory bodies, and stakeholders can review these virtual representations to evaluate compliance with building codes, zoning regulations, and aesthetic standards. This proactive approach can expedite approvals, reduce delays, and enhance overall project efficiency.
Overall, virtual reality is revolutionizing the house construction industry by improving design visualization, facilitating collaboration, enhancing the client experience, and streamlining the approval process. As VR technology continues to advance and become more accessible, its transformative impact on construction workflows and outcomes is poised to accelerate, driving innovation and efficiency across the industry.
Drones
Drones have emerged as a transformative technology in the house construction industry, offering a wide range of capabilities that are revolutionizing traditional construction processes. These unmanned aerial vehicles are equipped with cameras, sensors, and GPS systems, allowing them to perform tasks such as aerial surveys, progress monitoring, and data collection with unprecedented efficiency and accuracy.
One of the key benefits of drones in house construction is their ability to conduct aerial surveys and inspections. Traditionally, surveying a construction site involved time-consuming manual measurements and costly aerial photography. Drones can now fly over sites and capture high-resolution images, videos, and 3D models, providing detailed and up-to-date information about terrain, topography, and existing structures. This data is invaluable for site analysis, planning, and decision-making, enabling project teams to identify potential challenges, optimize layouts, and streamline construction workflows.
Moreover, drones play a vital role in progress monitoring and construction management. Project managers can use drones to track construction activities, monitor site progress, and assess work quality remotely. Real-time aerial footage allows for better visibility into project timelines, resource allocation, and adherence to schedules. Drones also facilitate communication and collaboration among stakeholders by providing visual updates and insights that enhance transparency, accountability, and decision-making throughout the construction process.
Additionally, drones improve safety and risk management on construction sites. They can access hard-to-reach or hazardous areas, reducing the need for workers to perform risky tasks manually. Drones can also conduct safety inspections, identify potential safety hazards, and monitor compliance with safety protocols. By enhancing safety practices and reducing accidents, drones contribute to a safer work environment and help mitigate project risks.
Furthermore, drones support environmental sustainability in construction by minimizing resource consumption and environmental impact. They can optimize logistics, monitor resource usage, and assess environmental conditions such as soil erosion or vegetation coverage. This data-driven approach enables more efficient resource management, reduces waste, and supports eco-friendly construction practices.
Overall, drones are revolutionizing the house construction industry by enhancing surveying and inspections, improving progress monitoring and management, increasing safety and risk mitigation, and promoting environmental sustainability. As drone technology continues to evolve and become more integrated into construction workflows, its transformative impact on efficiency, safety, and project outcomes is poised to revolutionize the industry further, driving innovation and progress in construction practices.
Robots
Robots are playing a transformative role in revolutionizing the house construction industry, offering a wide array of capabilities that enhance efficiency, precision, and safety in construction processes. These robotic systems are designed to perform various tasks traditionally done by human labor, ranging from bricklaying and welding to 3D printing and site automation, leading to significant advancements in construction workflows and project outcomes.
One of the key innovations in robotic construction is the development of bricklaying robots. These robots are equipped with advanced algorithms and robotic arms capable of precisely placing bricks in a predetermined pattern. Unlike manual bricklaying, which can be time-consuming and labor-intensive, robotic bricklayers work with speed and accuracy, reducing construction time and costs while ensuring consistent quality and structural integrity. This innovation has revolutionized the way walls and structures are built, offering unprecedented efficiency and productivity on construction sites.
Additionally, robots are being used for welding and assembly tasks in house construction. Welding robots are equipped with specialized tools and sensors that enable them to weld metal components with high precision and quality. This automation of welding processes not only improves efficiency and speed but also reduces errors and rework, leading to better overall construction outcomes. Similarly, assembly robots can handle repetitive tasks such as installing components or fittings, further streamlining construction processes and enhancing productivity.
Moreover, robotics is driving innovation in 3D printing technology for construction. 3D printing robots can fabricate building components and structures layer by layer using materials like concrete or plastic. This additive manufacturing approach allows for complex geometries and customized designs, opening up new possibilities for architectural creativity and construction flexibility. By automating the 3D printing process, robots are accelerating construction timelines, reducing material waste, and enabling the creation of sustainable and cost-effective buildings.
Furthermore, robots contribute to enhanced automation and site management in construction projects. Autonomous robots can navigate construction sites, transport materials, and perform tasks such as site cleaning or debris removal. These robots improve logistics, reduce manual labor, and enhance overall site safety by minimizing human exposure to hazardous conditions. Robotics also enables real-time data collection and analysis, providing valuable insights for project monitoring, decision-making, and optimization of construction processes.
Overall, robots are revolutionizing the house construction industry by automating tasks, improving precision and quality, accelerating construction timelines, reducing costs, and enhancing safety and sustainability. As robotic technology continues to advance and become more integrated into construction workflows, its transformative impact on efficiency, innovation, and project outcomes is poised to reshape the future of construction practices and standards.
Smart sensors, IoT (Internet of Things) devices, and AI (Artificial Intelligence)
Smart sensors, IoT (Internet of Things) devices, and AI (Artificial Intelligence) are revolutionizing the house construction industry by introducing a new level of automation, efficiency, and intelligence into building processes. These technologies work in synergy to enable real-time data collection, analysis, and decision-making, leading to optimized construction workflows, enhanced building performance, and improved user experience.
Smart sensors are embedded in various building components and systems to monitor parameters such as temperature, humidity, light levels, energy consumption, and structural integrity. These sensors continuously gather data and transmit it to centralized systems or cloud platforms, where AI algorithms analyze the data to derive insights and make informed recommendations. For example, smart sensors can detect anomalies in HVAC systems, identify potential maintenance issues, or optimize energy usage based on occupancy patterns, weather conditions, and user preferences.
IoT devices expand the capabilities of smart sensors by connecting them to a network of interconnected devices and systems within a building. IoT platforms enable seamless communication and integration among devices, allowing for centralized control, automation, and remote monitoring of building operations. For instance, IoT-enabled devices such as smart thermostats, lighting controls, security systems, and appliances can be managed and controlled remotely via smartphones or voice commands, enhancing convenience, energy efficiency, and security for homeowners.
AI technologies play a crucial role in harnessing the vast amounts of data collected by smart sensors and IoT devices. AI algorithms can analyze complex datasets, identify patterns, predict trends, and optimize processes in real time. In the context of house construction, AI-powered systems can assist in design optimization, predictive maintenance, energy management, and building performance optimization. For example, AI algorithms can analyze building designs to identify areas for improvement in energy efficiency or structural integrity, simulate different scenarios to evaluate design alternatives, and generate automated reports or recommendations for stakeholders.
One of the significant impacts of these innovations is the transformation of building management and maintenance practices. With smart sensors, IoT devices, and AI, building operators and facility managers can proactively monitor and manage building systems, identify issues before they escalate, schedule predictive maintenance tasks, and optimize resource usage. This proactive approach reduces downtime, extends equipment lifespan, minimizes energy waste, and enhances occupant comfort and satisfaction.
In conclusion,
Technology is completely changing how we build houses. With 3D printing, we can create entire structures layer by layer, making construction faster and more efficient. Virtual reality lets us step into a digital world to see and interact with our future homes before they’re even built, ensuring we get exactly what we want.
Drones are soaring above construction sites, capturing data and making it easier to manage projects and keep everyone safe. And robots are doing heavy lifting and intricate tasks, speeding up construction and improving precision. These innovations are making house construction smarter, more sustainable, and more exciting than ever before.
[…] construction process for piles varies depending on the type and material. Driven piles are pre-manufactured from steel, […]